Every day, we process a couple of tons of food, literally. Most of this food shows up in its original wholesale packaging. That means it’s in boxes of some sort.
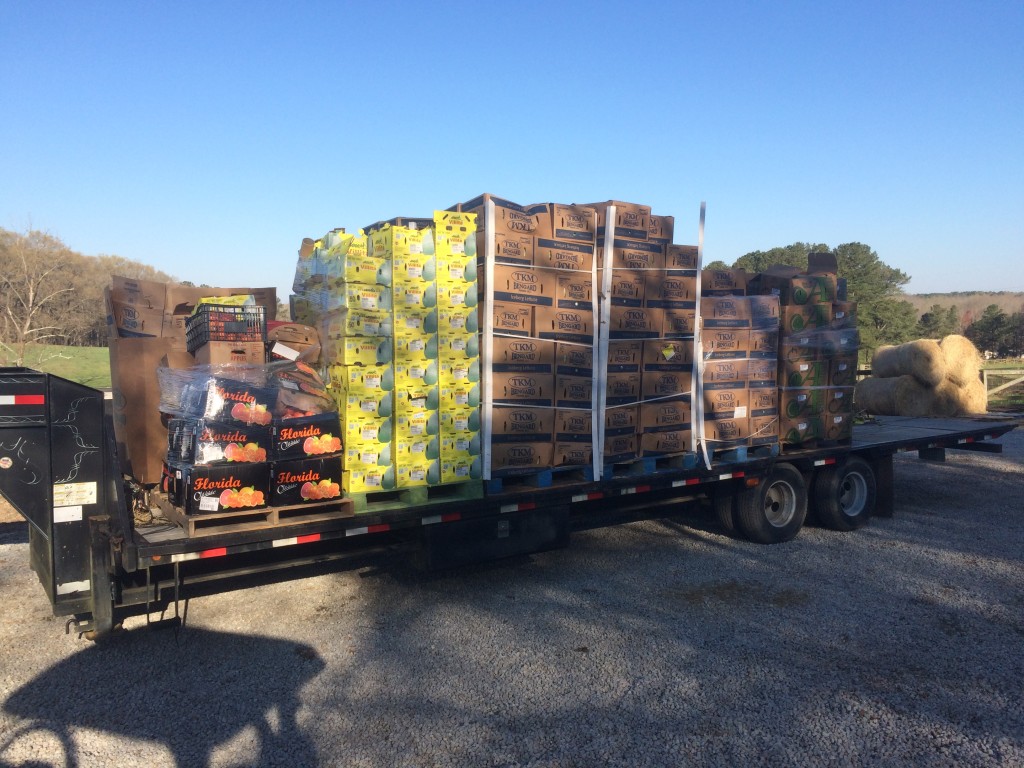
This is a good example of what I’m talking about. Oranges, avocados, lettuce, etc. Each box holds what will be food for our animals. So what happens when the food is removed from all these boxes? We get a huge pile of boxes, every day. This whole produce thing started out small, so our solution was small. We just tossed the boxes into our burn barrel where we’ve burned all of our paper trash all the years I’ve lived on the farm. As the business grew, we built a bigger burn barrel, and then a bigger one, but the solution itself didn’t change. I did contact Waste Industries to see if we could recycle the cardboard but it sounded like they basically treated it as trash and charged us to boot. Then Miguel had an idea.
“Jefe, the guy who owns El Toro has a compactor where he compacts his cardboard. He must sell it to pay for the compactor.”
Turns out Miguel was right. He went and talked to the owner of El Toro and while he didn’t get rich, he was able to pay for his compactor in a few years and get a few dollars to spare. Armed with this information I started looking at compactors, and ran into a brick wall. Turns out they all run on three phase power and we only have single phase power on the farm. So I looked closer at compactors. Turns out they are just a simple hydraulic system running at about 2500 psi. There isn’t any fancy computer on most of them, just some safety lockouts and a big honking electrical motor to turn a hydraulic pump.
Since our log splitter is one that I built myself and it has no hydraulic system or gas engine but instead runs off of our skid steer quick connects, I have some experience using an outside power source for hydraulic power. And our skid steer runs at about 2500psi. With about a 65 horse power engine, we should have plenty of power to run a baler. The issue was to find one that is ragged out so badly it’ll be cheap enough I can justify hacking all the expensive bits off of it. No sense buying a $1000 hydraulic system just to cut it off. So I talked to my local cardboard recycler and told him my plan. He said he knew a guy in Virginia who might have just what I want, and he was right. Yesterday I came home with this.
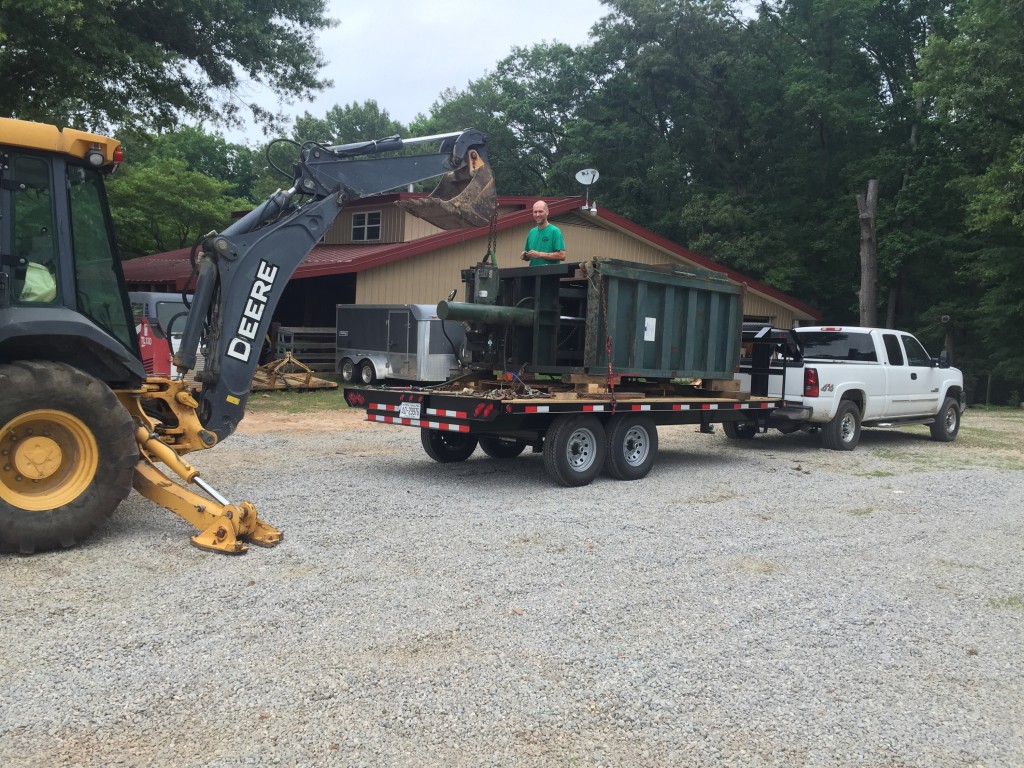
After looking at balers for a while, it seemed they all were about the same. 60″ vertical baler, 10hp motor, yadda yadda. I went up to look at this baler and made sure the cylinder looked ok, that the door opened and closed, etc. It had the manufacturer’s name on it, but not the model so I could only get an approximation of what it was. The electrical system was shot and I was removing the hydraulics so it really didn’t matter about the rest of it. It wasn’t till I got it home that I looked up the motor specs and found out this is the Philadelphia Tram Rail Company’s 7200HD when what I thought it was was the 3400HD. Oops. Turns out it weighs over 8000 pounds where I thought it weighed 5000 pounds. Also it makes 1800 pound bales vs 1200 pound bales with its 115,000 pounds of compression force! Considering I bought this thing for about what it is worth at a scrap yard, I don’t feel too badly about getting the hoss unit, but it was an adventure getting it off of the trailer and into position.

It took both the crane and the backhoe to lift this thing. The crane will pick up 21,000 pounds but that is at max lift in the best position. Our where we had to work, we could pick up about 6000 pounds, which is about 2000 short of what we needed.
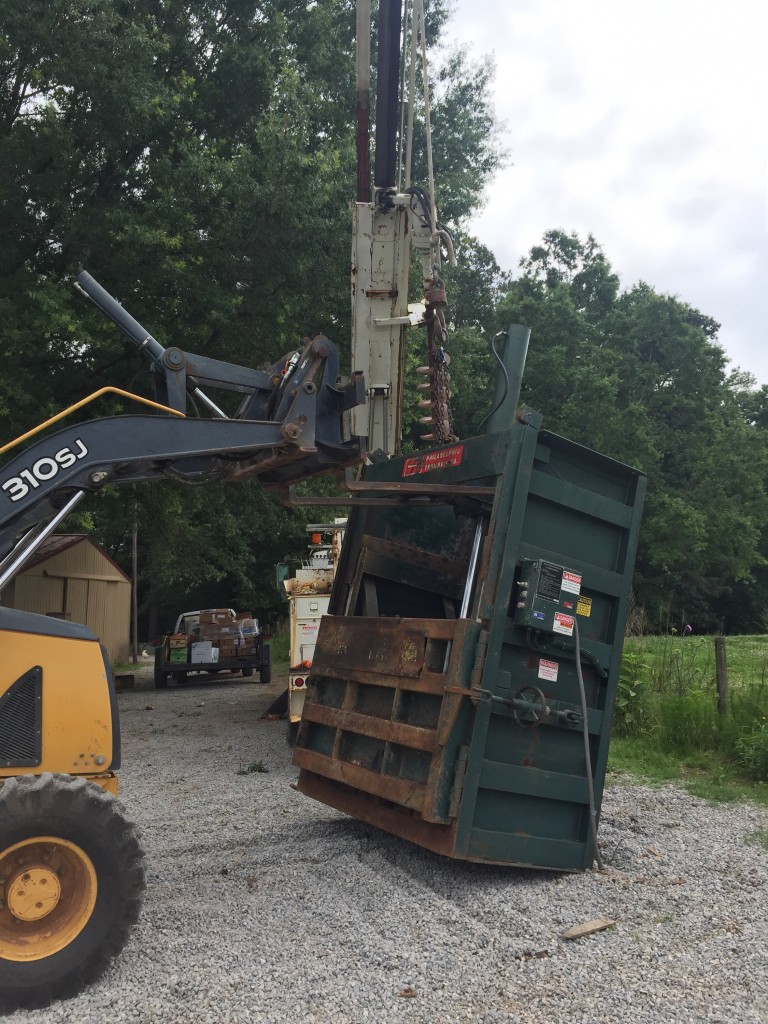
Since we didn’t have a concrete pad poured yet, we had to be careful and not drag the baler, creating an uneven footing.

It took Miguel, Vicente, and me, along with the crane truck, the backhoe, the farm tractor, the skid steer, and the diesel truck and the new trailer all involved to get this job done. Plus it took almost every chain we had, two come-alongs, many blocks of wood, and too much of the morning. Now I have to plumb in the new hydraulic setup, grease the door, find wire ties for making bales, and finally put this thing to work. If everything works as expected, then we can pour a concrete pad and move this thing all over again! But then we’ll be baling our cardboard instead of burning it which should save time and a little bit of the world.