
This article is really written for my fellow farmers out there, or people who like to tinker. Yes it is farm related, very much so. But this is about the technical side of farming, and how we keep our products cold and safe while being transported from the processor or from other farms.
When I first started getting serious about moving meat for the farm, I had a friend (Hey Paul!) who had a truck that was sitting idle. It was an International medium duty reefer truck that had come back in from lease and was just sitting. Since we’d put about (literally) 1.5 million miles on a truck pretty much just like it at my old company, I felt pretty good about running a truck like this for the farm. It would cool to 20 F and I was more than familiar with the operation and maintenance, so I bought it. For the past four years or so, this has been how we’ve moved meat, eggs, milk, cheese, etc everywhere.
Most farmers like myself just put some coolers in the back of the truck and figure it’ll be ok. But I never trusted coolers. What if I get stuck in traffic (it happened), what if I break down on the road in the summer (it happened). I have 600 pounds of meat, or 30 gallons of milk going bad in a cooler. Nope, I like the box truck and how it cooled itself down, independent of ice or time.
But after four years of running this truck, I’ve realized that it is simply too big for what we need. When fully loaded, with all the goodies from all the farms, everything was single stacked with room to walk around. We were not utilizing 90-95% of the space we were cooling.
Also there is a failing of the particular model cooler that I had. During the summer, if you are sitting still, it tends to overheat the reefer engine and shut down. Not a problem when you are moving, and not a problem period because I just get everything cold and then turn the cooler off when I stop to load. As I leave, I turn it back on and it quickly recools everything. But it always made me nervous that maybe it would shut down when I wasn’t prepared for it.
Plus, the fuel and maintenance bills for a large truck are, well, large. The oil costs more. The filters cost more. The belts cost more. What I needed was a different solution. One that costs less to own and maintain.
Our chicken farmer, Brittany Ridge, has a truck with a dedicated cooler in the bed. It is run from a compressor hooked to the engine. Crank the truck, the box cools. Turn the truck off, the box is a big igloo cooler. It seems to work very well and I was quite jealous. I looked for a solution similar to theirs for a year or so, to no avail.
I know some other farmers have pull behind trailers that they use. They mount a generator to the trailer and run freezers from the generator. Pretty much the same thing that food trucks do so they have kitchen power on the truck. As long as the generator works, then everything is cooling. This would also let me use my existing truck which is really nice. The radio plays my station. The seat fits my butt. That kind of thing. It’s also nice because you can back the trailer up to a building and pull a drop cord and run the freezers from that, saving the generator. That would help when we have a big load of meat like when turkeys show up for Thanksgiving, or someone orders 1/2 of a cow. We could just leave things in the trailer and cool down or freeze depending on what we need.
I wondered about insulating a trailer and putting a CoolBot in to keep things cool. I utilize a CoolBot in our walk in cooler here on the farm. It does fine to keep things cold, but I wasn’t sure about keeping things frozen. Plus I’d need to put a window unit in the trailer, then drag it up and down the highway a lot of miles. That means that some day, that window unit that was designed to sit still is going to bounce one time too many and break. That could be a very bad day. Nah, I needed something with some redundancy.
When I was at Chaudhry’s dropping off a cow, I saw they had a flier for someone selling a used cooler trailer. It had an actual compressor and cooling, not a CoolBot. It looked pretty serious. And used it was $20,000 asking price! Yikes! That is WAY too much. So I was back to freezers and a generator.
I purchased a trailer (harder than you’d think) and then bought three chest freezers that would fit well and hold what I needed from Lowes.

I made metal corner brackets that would hold the freezers in place, and secure them to the floor. But as I was working on this project, I had another thought. Just how much power does it take to run three chest freezers? They are pretty efficient. Why couldn’t I run them from an inverter?
I hooked all three freezers up to my Honda 2000 watt generator and low and behold, it ran them just fine. Usually you do a power calculation, but I had a generator sitting right there so that was the quick and easy solution (the calculation said 1800 watts, btw, when I ran it later).
So if 2000 watts would run the freezers, what did I need for a bit of headroom and future expansion? Looks like Amazon sells a 3000 watt inverter at a good price. Click. Done.

I installed the inverter, with heat shield, and it’s associated 2/0 gauge wiring. (Don’t you just love drilling holes in something brand new? Ugh, me either. But it worked out nicely and looks good.) I routed the cables from the freezers to a central power strip, and then moved to the front of the trailer.

Here I had some issues. Everybody sells V nose trailers now. But I needed room for what I thought then would be my generator but was now my batteries. Finally I found a flat nosed trailer the right size and I had this tongue area to work with. I routed the cabling from the inverter to the batteries, but only after welding on and reinforcing a battery platform with retention. A good bit of wiring, soldering on connectors, etc. and I was able to hit the on button.

So I could run my freezers from my batteries. But that is only half the battle. Now I wanted to recharge the batteries from my truck, which is already merrily producing electricity as I drive. I looked at battery isolators of all varieties. I knew about them from my teenage job as a car stereo installer and also from boats. But I wasn’t really excited about how they worked. Then I came across something I’d never heard of before, an automatic charging relay or ACR. One side goes to the truck electrical system, one side goes to the trailer. It does the smart work in between. Couldn’t be simpler.
So I ordered 50 feet of 2/0 gauge cabling and set about installing the ACR, circuit breakers, quick connect plugs, fuses, and auxiliary grounds. After some troubleshooting (it’s called reading the instructions and doing that part you skipped) I got the ACR online.
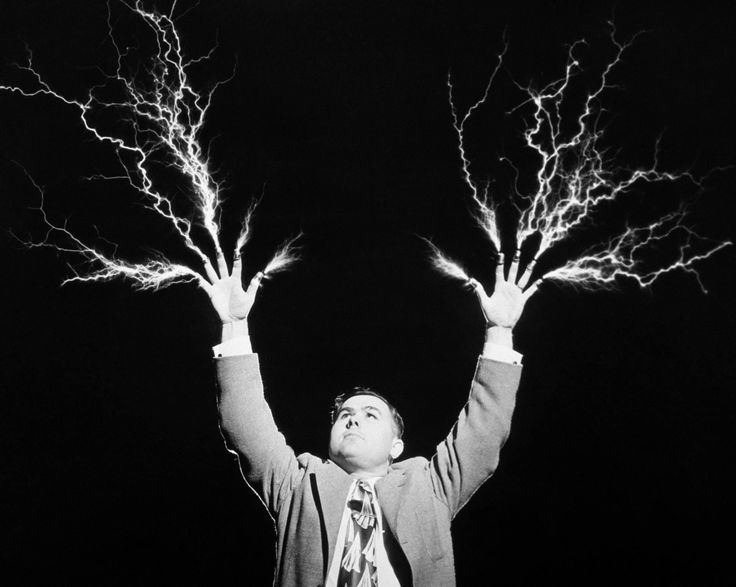
That’s pretty much how I felt.
Thursday was the first day I used the new setup. I hooked the trailer up, which takes about .2 extra seconds with the electrical connections. I cranked my truck and watched the volt meter first show the recovery from cranking. Once it hit about 13.5 volts, it dipped back to 13.0 as the ACR switched over and bridged the trailer to the truck batteries. About 20 seconds later, it came back up to its normal 14 volt range and then maintained it for the ride to my first stop.
At one of my stops, I hopped out of the truck and purposefully took my time, giving the freezers about 30 minutes to run on battery power alone. When I cranked the truck, it was the same story. First recover the starting battery, then the ACR bridges, then about a minute before we were back to 14 volts. 30 minutes of run time is recharged in one minute? So several hours of run time will fully recharge before my next stop easily? It truly does work well. This means I can stop for lunch (remember how the box truck couldn’t run when stopped?) or spend a few extra minutes talking to a farmer without worrying about my product on board. It’s not only still cold, it’s actually freezing it down to temp which is an issue sometimes as I get fresh product that hasn’t been frozen yet.

The best part is everything is off the shelf (or off the web) standard stuff. No having to call a repair man or, heaven forbid, having to go to ThermoKing to get anything done. If a freezer dies, it’s still a heck of a cooler to get me through the day and I can stop at pretty much any store and buy a chest freezer off of the floor. Truck stops carry inverters. The ACR is solid state. Everything else is basically wiring. And the best part is I sold the box truck for about double what I have in this entire setup and the maintenance going forward is almost zero. No I don’t have the capacity of the box truck anymore, but that wasn’t a problem to start with.
We’ll see how this setup does over the years, it it can survive the harshness of driving up and down the road, but for now I couldn’t be happier.
Except I have to decide if I’m going to decal the trailer with our farm logo and info. That part hasn’t been decided.